In the modern manufacturing and construction landscapes, sealing solutions are undergoing a renaissance, fundamentally fuelled by the pivot towards customization.
Custom other sealing strips are emerging as invaluable assets across various industries. These specialized strips, tailored to specific needs, address gaps that conventional sealing products fail to fill, thereby enhancing efficiency, durability, and performance standards.
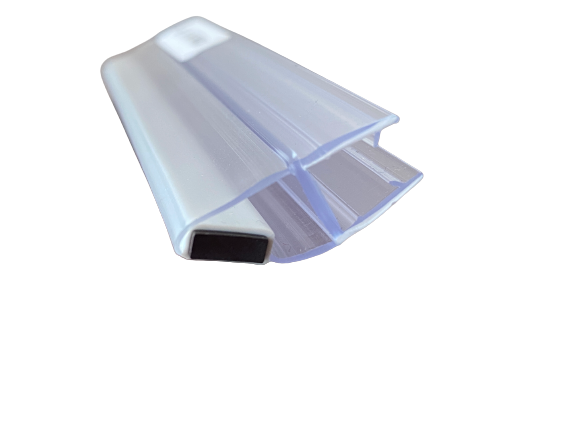
Delving into the realm of custom other sealing strips reveals a world where precision engineering meets innovative materials science. These sealing strips are uniquely designed to meet diverse application demands, from automotive and aerospace to housing and renewable energy structures. Unlike generic sealing solutions, custom other sealing strips are crafted with specific dimensions, material compositions, and performance parameters, offering a more reliable fit and function.
From a technical perspective, the customization process begins with a thorough analysis of the operating environment and performance requirements. Understanding the exact conditions to which the sealing strip will be exposed—such as temperature extremes, chemical exposure, mechanical stress, and environmental factors—guides the selection of materials. Experts often choose among silicone, EPDM, neoprene, and other high-performance polymers that offer superior resilience and adaptability. By harnessing the unique properties of these materials, custom sealing strips can provide exceptional weatherproofing, noise reduction, vibration dampening, and thermal insulation.
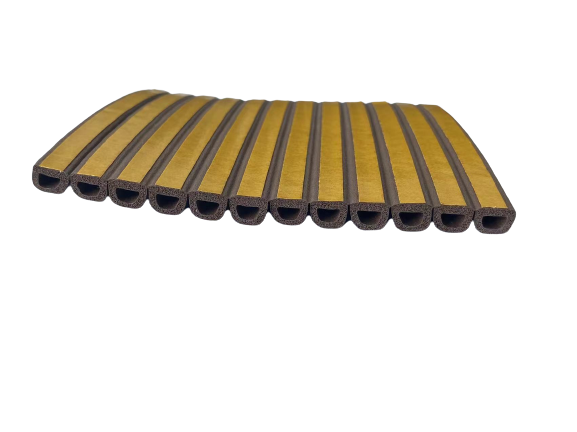
The expertise involved in the design and manufacture of these strips cannot be overstated. Professionals in this field harness advanced computer-aided design (CAD) software and precision manufacturing techniques, such as extrusion, molding, and adhesive application, to create sealing solutions that conform perfectly to their intended applications. This meticulous attention to detail not only ensures optimal performance but also extends the lifespan of both the strips and the devices or structures they are used on.
custom other sealing strips
Authoritativeness in this arena is underscored by rigorous testing and quality assurance processes. Industry standards such as ASTM and ISO provide benchmarks for material and performance testing, ensuring that custom other sealing strips meet or exceed customer expectations. This adherence to established standards and practices enhances trust and positions companies as leaders in sealing technology.
Moreover, reliability and environmental sustainability are increasingly significant to both manufacturers and end-users, contributing to the trustworthiness of custom sealing strips. Many companies are now implementing environmentally friendly manufacturing processes and sourcing materials from suppliers that adhere to ecological best practices. This commitment to sustainability not only reduces the environmental impact but also resonates with eco-conscious consumers.
In terms of practical experience, businesses adopting custom other sealing strips have reported marked improvements in operational efficiency and product longevity. For instance, in the automotive sector, these seals are pivotal in enhancing vehicular aerodynamics and mitigating water ingress, leading to improved performance and reduced maintenance costs. In residential construction, custom seals are instrumental in achieving stringent energy efficiency standards, keeping homes insulated from extreme weather conditions while lowering energy consumption.
In conclusion, custom other sealing strips represent the future of sealing solutions in various industrial applications. Their ability to offer precise, reliable, and sustainable performance makes them an indispensable component in the design and manufacture of modern products and infrastructure. By investing in these customizable solutions, companies can ensure they remain at the forefront of innovation, delivering superior performance and customer satisfaction.